5 Reasons to Document Business Process Flows During ERP Design
Every ERP project has a significant phase which involves figuring out how the new ERP system will need to be built to meet the functional requirements of the organisation in which it will be deployed. This phase goes by different names depending on the ERP product and system integrator, for example, analysis and design, system design, blueprinting, etc. and arguably is the most important part of an ERP project, since all other phases depend on it to one extent or another.
Traditionally, this phase of the project culminated in a set of design documents that required sign-off from the business before system build could begin. In recent years, many ERP projects have adopted an iterative design/build process during this phase based on agile principles, which again ultimately will require business sign-off.
Click Play for a 40 second video summary of this blog 5 Reasons to Document Business Process Flows During ERP Design.
We have found that in many ERP projects, even though the design sign-off is achieved, there is often a poor understanding of how the new ERP system is actually going to work, certainly outside of the core project team. We believe that there is a very strong case for investing the time and effort to document the new design in the form of swimlane-based business process flows. Here are five reasons why.
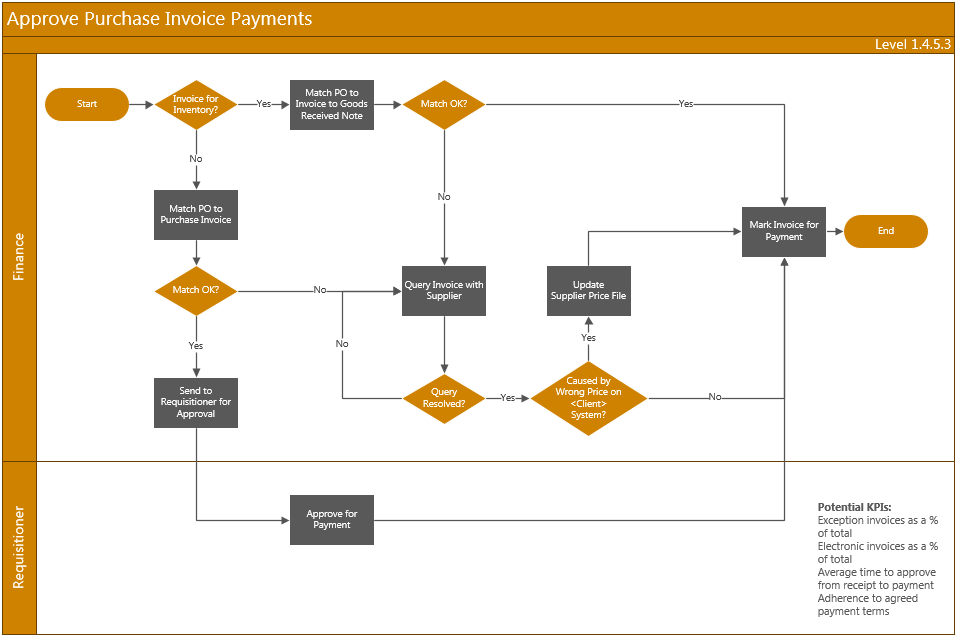
1. Improved project team understanding
The exercise of building process flow diagrams forces the ERP project team to really think about how the different business processes will work in future. The includes the connection to systems and processes that may exist outside of the ERP. In our experience, building the process flows will sometimes even identify points that have been missed during the design process.
2. Better communication to the business
One of the flaws with ERP design processes is that business stakeholders who are not directly involved in the project will often struggle to understand how the new system is going to work. This is a real problem when those same stakeholders are expected to sign off the designs. Having well-documented end-to-end process flow diagrams brings the new design to life and helps people to understand how business processes will work in future.
3. More effective change management
Because the process flow diagrams help the business to better understand how processes will be different in future, they also help considerably when identifying the impacts that the new system and processes will have on existing roles in the organisation. This is particularly the case when the new design will result in business process automation or centralisation of activities or where new processes are required.
4. Easier development of test scripts
During the test phase of the project, the new system will need to be methodically tested using scripts. Often, creating these test scripts is a real struggle for the ERP project team and it is difficult to link them together coherently so that testing is done in an end-to-end manner for each process. Having documented process flows available makes all of this much easier, as there is a framework on which to base the scripts.
5. More effective training
Training users is one of the final and most important steps in the ERP implementation process. For training to be really effective, it’s important to have good quality training material, which relates the different elements of the system to process steps that users can recognise. Documented business process flows provide a structure and context for the development of training material and the delivery of training to end users.
In summary, we believe that documenting business process flows is a really important step in completing the design stage in ERP projects.
This blog was written by Sean Jackson, Principal Consultant at Lumenia. If you would like to learn more about this topic and how Lumenia can help you document your Business Process Flows During ERP Design or for any other aspects of ERP please send an e-mail to Sean Jackson.